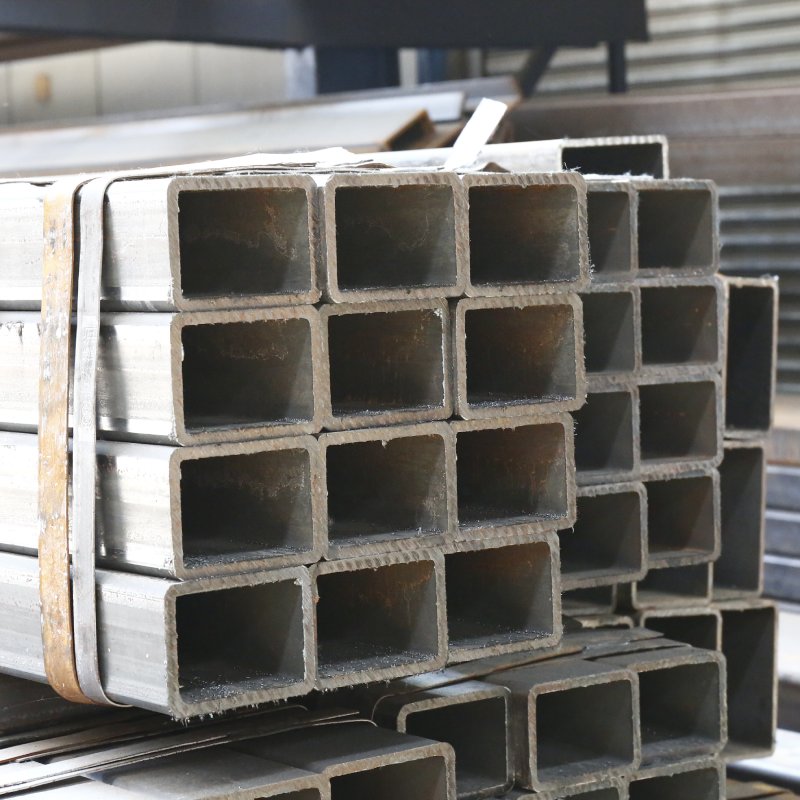
Image source Aiweiblockmachine
Incorporating Digital Twins and Simulation for Production Optimization in Block Manufacturing
Title: Harnessing Innovation: Incorporating Digital Twins and Simulation for Production Optimization in Block Manufacturing
Introduction:
The block manufacturing industry, a vital player in the construction sector, is continually evolving, with technological innovations driving efficiency and sustainability. One such groundbreaking technology that has gained traction is the use of digital twins and simulation in production optimization. In this article, we will explore the transformative potential of digital twins and simulation for block manufacturing, examining their applications, benefits, and the steps involved in integrating these technologies into the production process.
Understanding Digital Twins and Simulation:
1. Digital Twins: Digital twins are virtual replicas of physical objects or systems. In the context of block manufacturing, a digital twin represents a comprehensive digital model of the entire production process, from raw material inputs to the finished block. This virtual representation allows for real-time monitoring, analysis, and optimization.
2. Simulation: Simulation involves the creation of computer models that mimic real-world processes. In block manufacturing, simulation allows manufacturers to predict and analyze the behavior of the production process under various conditions. This predictive capability is invaluable for optimizing operations and making informed decisions.
Applications in Block Manufacturing:
1. Production Process Visualization: Digital twins provide a visual representation of the entire block manufacturing process. This visualization includes every step, from raw material preparation to curing and packaging. This visual insight allows for a comprehensive understanding of the production workflow.
2. Predictive Analysis for Quality Assurance: Simulation tools enable predictive analysis of the production process, allowing manufacturers to anticipate potential issues and optimize parameters for quality assurance. By simulating various scenarios, the digital twin can highlight potential defects, allowing for proactive adjustments before actual production.
3. Resource Optimization: Digital twins and simulation models enable efficient resource allocation. By analyzing the impact of different resource configurations, manufacturers can optimize energy usage, raw material consumption, and overall resource efficiency, leading to cost savings and sustainability benefits.
4. Process Monitoring and Control: Real-time monitoring through digital twins facilitates better control over the production process. Any deviations from optimal conditions can be identified and addressed promptly, minimizing the risk of defects and ensuring consistent quality in the final product.
5. Equipment Performance Optimization: Simulation tools can be used to model and optimize the performance of manufacturing equipment. This includes assessing the efficiency of block-making machines, curing systems, and material handling equipment. Optimizing equipment performance enhances overall production efficiency.
6. Batch and Production Planning: Digital twins assist in batch and production planning by providing insights into the optimal production schedules. Simulation models can account for varying demand, raw material availability, and production constraints, allowing manufacturers to plan efficiently and reduce idle time.
Benefits of Digital Twins and Simulation in Block Manufacturing:
1. Improved Efficiency: The real-time monitoring and predictive capabilities of digital twins contribute to improved operational efficiency. Manufacturers can identify bottlenecks, streamline workflows, and optimize resource utilization for maximum output.
2. Enhanced Quality Control: By simulating the production process, manufacturers can identify potential quality issues before they occur. This proactive approach to quality control ensures that the final blocks meet or exceed desired standards, reducing waste and enhancing customer satisfaction.
3. Cost Reduction: Optimizing resource usage, energy consumption, and production schedules through digital twins can lead to significant cost reductions. The ability to identify and address inefficiencies in real-time contributes to overall cost-effectiveness.
4. Sustainable Practices: Digital twins enable manufacturers to adopt more sustainable practices. By optimizing resource usage and minimizing waste, block manufacturing companies can align their operations with environmental stewardship goals and meet the increasing demand for eco-friendly products.
5. Faster Time-to-Market: Simulation tools allow manufacturers to test and iterate production processes more quickly in the virtual environment. This accelerates the product development cycle, reducing time-to-market for new block variants or production optimizations.
6. Data-Driven Decision-Making: Digital twins generate a wealth of data about the production process. This data, when analyzed, provides valuable insights for data-driven decision-making. Manufacturers can make informed choices about process adjustments, equipment upgrades, and overall production strategies.
Steps to Integrate Digital Twins and Simulation in Block Manufacturing:
1. Define Objectives and Key Performance Indicators (KPIs): Clearly define the objectives of integrating digital twins and simulation in block manufacturing. Identify key performance indicators (KPIs) that align with production optimization goals, such as improved efficiency, reduced waste, or enhanced quality.
2. Select Appropriate Simulation Software: Choose simulation software that aligns with the specific needs of block manufacturing. The selected software should be capable of modeling the entire production process, including material handling, mixing, molding, curing, and packaging.
3. Develop a Digital Twin of the Production Process: Create a digital twin that accurately represents the block manufacturing process. This involves mapping out each step of the process, incorporating data on raw materials, equipment specifications, and environmental conditions. The digital twin should mirror the real-world production environment as closely as possible.
4. Implement Real-Time Monitoring Systems: Integrate real-time monitoring systems into the production process to feed data into the digital twin. This could include sensors on equipment, monitoring the temperature and humidity of curing chambers, and tracking material flow. The data collected enhances the accuracy and effectiveness of the digital twin.
5. Conduct Simulation Experiments: Use the simulation software to conduct experiments and analyze the performance of the production process under various conditions. This could involve adjusting parameters such as curing time, material composition, or machine settings to identify optimal configurations.
6. Optimize and Iterate: Based on the simulation results, optimize the production process to achieve the desired goals. Iterate on the digital twin, making adjustments and refinements to continually improve efficiency, quality, and resource utilization.
7. Train Staff on Digital Twin Utilization: Ensure that staff members involved in the production process are trained on the utilization of the digital twin and simulation tools. Familiarity with these technologies empowers employees to actively contribute to the optimization efforts.
8. Continuously Monitor and Update: Implement a system for continuous monitoring of the production process and regularly update the digital twin based on real-world data. This ensures that the virtual model remains accurate and continues to provide meaningful insights for ongoing optimization.
Challenges and Considerations:
1. Initial Investment: The integration of digital twins and simulation tools may require an initial investment in software, sensors, and training. However, the long-term benefits in terms of efficiency, cost reduction, and sustainability often outweigh the upfront costs.
2. Data Security and Privacy: Managing data security and privacy is crucial, especially when implementing real-time monitoring systems. Manufacturers must ensure that sensitive production data is protected from unauthorized access or cyber threats.
3. Staff Training and Adoption: Staff members may require training to understand and effectively use digital twins and simulation tools. A comprehensive training program is essential to maximize the benefits of these technologies.
4. Integration with Existing Systems: Integrating digital twins with existing production systems and software can be a complex task. Compatibility and seamless integration are key considerations to avoid disruptions in operations.
5. Model Accuracy and Validation: The accuracy of the digital twin depends on the precision of the model and the data used to create it. Continuous validation against real-world production data is necessary to ensure that the virtual model reflects the actual manufacturing environment.
Case Studies: Successful Implementation of Digital Twins in Block Manufacturing
- Optimizing Curing Processes: Case Study: A block manufacturing company implemented digital twins to optimize curing processes. By simulating different curing time and temperature scenarios, the company identified the optimal conditions for achieving maximum strength and durability in the blocks. This led to reduced curing times, energy savings, and enhanced product quality.
- Efficiency Enhancement in Material Handling: Case Study: A block manufacturing plant utilized digital twins to optimize material handling processes. Simulation experiments helped identify the most efficient layout for material storage and transportation, reducing idle time and streamlining production workflows.
Future Trends and Developments:
1. Integration with Industry 4.0: The integration of digital twins and simulation in block manufacturing aligns with the broader trend of Industry 4.0. As smart factories become more prevalent, the seamless connectivity and data exchange facilitated by Industry 4.0 principles will further enhance the capabilities of digital twins.
2. Artificial Intelligence (AI) and Machine Learning (ML): The incorporation of AI and ML algorithms into digital twin models will enable more advanced predictive analytics. These technologies can learn from historical data, identify patterns, and make real-time adjustments to optimize production processes.
3. Remote Monitoring and Control: The use of digital twins for remote monitoring and control is expected to grow. Manufacturers can remotely assess the performance of the production process, make adjustments, and ensure optimal efficiency, reducing the need for on-site interventions.
Conclusion:
Incorporating digital twins and simulation into block manufacturing processes represents a paradigm shift towards more intelligent, efficient, and sustainable production. The ability to visualize, analyze, and optimize the entire production process in a virtual environment empowers manufacturers to make informed decisions that positively impact efficiency, quality, and resource utilization. As the industry continues to embrace technological advancements, the integration of digital twins and simulation stands at the forefront, promising a future where block manufacturing is not only resilient but also at the forefront of innovation in the construction sector.