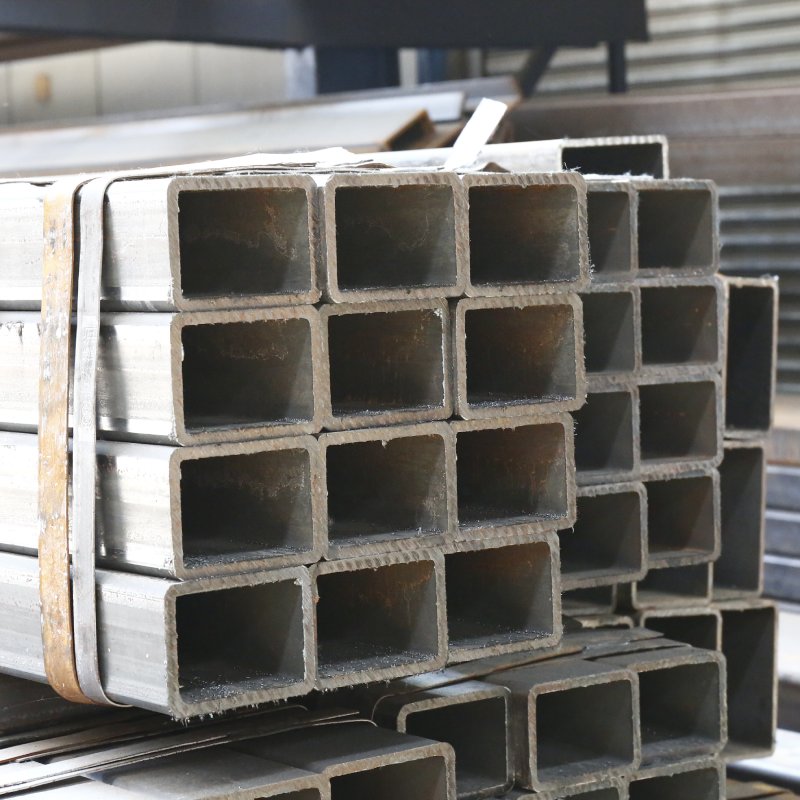
Image source Aiweiblockmachine
Title: Digital Transformation and the Crucial Role of Data Analytics in Full-Automatic Production Lines
Introduction
In the era of Industry 4.0, digital transformation has become a driving force behind the evolution of manufacturing processes. Full-automatic production lines, marked by their high efficiency and minimal human intervention, are at the forefront of this transformative journey. One of the key elements propelling this change is data analytics. This article delves into the significance of data analytics in the context of full-automatic production lines, exploring how it contributes to enhanced efficiency, improved decision-making, and overall operational excellence.
1. **Data Generation in Full-Automatic Production Lines**
Full-automatic production lines are characterized by the integration of sophisticated machinery, sensors, and control systems that generate vast amounts of data. Every aspect of the production process, from raw material input to the final product’s output, is captured by sensors and devices. This data deluge provides a wealth of information that, when harnessed effectively, can drive optimization and innovation in manufacturing.
2. **Real-Time Monitoring and Control**
Data analytics in full-automatic production lines enables real-time monitoring and control. Sensors embedded in the production machinery continuously collect data on variables such as temperature, pressure, speed, and quality parameters. By analyzing this data in real time, manufacturers gain insights into the performance of each component in the production line.
Immediate access to this information allows for proactive decision-making. If a deviation from the optimal operating conditions is detected, adjustments can be made in real time to prevent potential issues or disruptions. This not only minimizes downtime but also ensures that the production line operates at peak efficiency.
3. **Predictive Maintenance for Increased Uptime**
One of the significant advantages of data analytics in full-automatic production is the ability to implement predictive maintenance strategies. By analyzing historical data on equipment performance and failure patterns, machine learning algorithms can predict when a particular component is likely to fail. This foresight enables manufacturers to schedule maintenance activities precisely when needed, avoiding unnecessary downtime and extending the lifespan of machinery.
Predictive maintenance is a paradigm shift from traditional reactive approaches, reducing the reliance on scheduled maintenance and minimizing the risk of unexpected breakdowns. As a result, full-automatic production lines become more reliable and cost-effective.
4. **Optimizing Production Processes with Data Analytics**
Data analytics plays a pivotal role in optimizing the entire production process. Through the analysis of historical and real-time data, manufacturers can identify inefficiencies, bottlenecks, and areas for improvement. This insight allows for data-driven decision-making to streamline processes, reduce waste, and enhance overall efficiency.
For example, data analytics can uncover correlations between specific operating parameters and product quality. By adjusting these parameters in real time, manufacturers can consistently produce high-quality products, meeting or exceeding customer expectations. This optimization not only improves product quality but also contributes to resource efficiency and cost reduction.
5. **Quality Control and Defect Prevention**
Data analytics contributes significantly to quality control in full-automatic production lines. By analyzing data related to product specifications, sensor readings, and historical quality data, manufacturers can implement advanced analytics models for defect prediction and prevention.
Machine learning algorithms can identify patterns associated with product defects and deviations from quality standards. This predictive quality control approach enables manufacturers to take preemptive measures to correct issues before they result in the production of defective goods. As a result, the overall quality of the manufactured products is improved, leading to higher customer satisfaction and reduced waste.
6. **Enhancing Flexibility and Adaptability**
Full-automatic production lines equipped with data analytics capabilities become more flexible and adaptable to dynamic market demands. By continuously analyzing market trends, demand forecasts, and production data, manufacturers can adjust production schedules and configurations in response to changing requirements.
This adaptability is particularly crucial in industries where product variations and customization are common. Data analytics enables manufacturers to optimize production lines for different product specifications without the need for extensive reprogramming or manual intervention. This flexibility enhances responsiveness to market demands and strengthens the competitive position of manufacturers.
Conclusion
In the realm of full-automatic production lines, digital transformation powered by data analytics is a game-changer. The ability to harness and analyze data in real time not only optimizes operational efficiency but also enhances decision-making, predictive maintenance, and overall product quality. As manufacturers continue to embrace Industry 4.0 principles, the role of data analytics in full-automatic production lines will become increasingly central to achieving and sustaining competitive advantages in the rapidly evolving landscape of modern manufacturing.