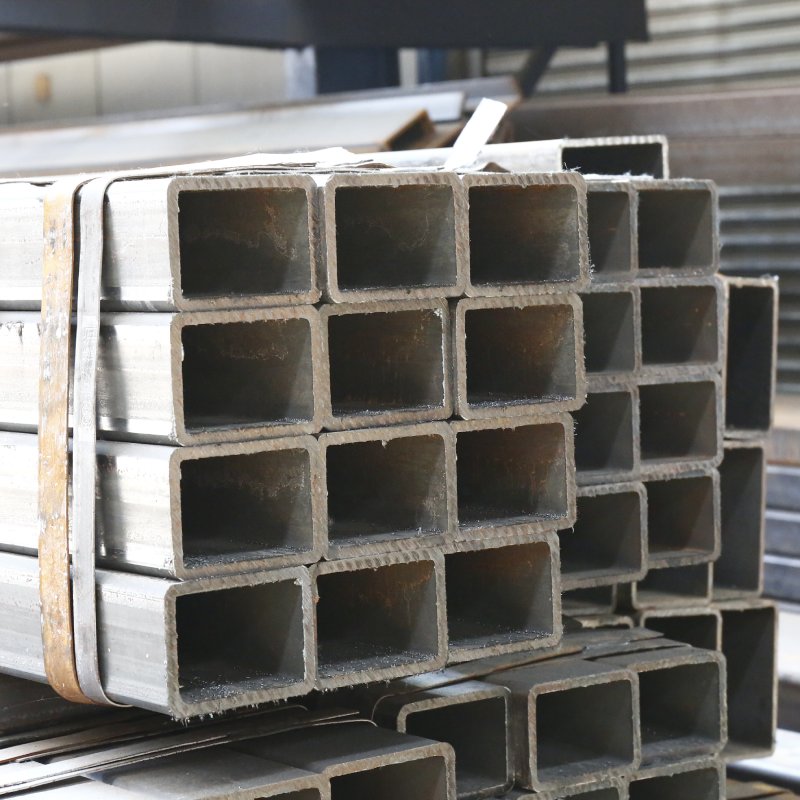
Image source Aiweiblockmachine
Cybersecurity Measures for Protecting Full-Automatic Block Production Systems
Title: Safeguarding Innovation: Cybersecurity Measures for Full-Automatic Block Production Systems
Introduction
In the era of Industry 4.0, where automation and connectivity reign supreme, full-automatic block production systems have become vital assets in the manufacturing landscape. However, with this increased connectivity comes the pressing need to fortify these systems against potential cyber threats. This article explores the essential cybersecurity measures that manufacturers must implement to protect full-automatic block production systems, ensuring the integrity, confidentiality, and availability of critical production processes.
1. **Network Segmentation and Isolation**
The first line of defense against cyber threats in full-automatic block production systems is network segmentation. By dividing the network into isolated segments, manufacturers can limit the lateral movement of cyber threats. Critical production systems should be separated from general IT networks to prevent unauthorized access to sensitive machinery and data.
Isolation ensures that even if one part of the network is compromised, the impact is contained, and the core production systems remain secure. Implementing firewalls and access controls between network segments enhances the overall resilience of the system.
2. **Robust Access Controls and Authentication Mechanisms**
Securing access to full-automatic block production systems begins with implementing robust access controls. Role-based access should be enforced, ensuring that only authorized personnel have access to specific functions and data. Multi-factor authentication adds an additional layer of security, requiring users to verify their identity through multiple means, such as passwords and biometrics.
Regularly reviewing and updating access permissions is crucial, especially as personnel roles and responsibilities change. This ensures that only individuals with a legitimate need have access to sensitive production systems.
3. **Continuous Monitoring and Anomaly Detection**
Continuous monitoring of network traffic and system logs is imperative for early detection of potential cyber threats. Implementing advanced anomaly detection systems allows manufacturers to identify unusual patterns or behaviors within the network that may indicate a security incident.
Machine learning algorithms can be employed to analyze normal system behavior and automatically detect deviations that could signify a cyber attack. Real-time monitoring enables prompt responses to security incidents, minimizing potential damage.
4. **Regular Software Updates and Patch Management**
Full-automatic block production systems often rely on software and firmware to function optimally. Regularly updating and patching this software is essential for addressing known vulnerabilities and ensuring that the system is fortified against the latest cyber threats.
Manufacturers should establish a rigorous patch management process, regularly reviewing and applying updates to both operating systems and application software. Automated patch deployment tools can streamline this process, reducing the window of vulnerability.
5. **Data Encryption and Secure Communications**
Securing the communication channels within full-automatic block production systems is critical for protecting sensitive data from interception or tampering. Implementing end-to-end encryption ensures that data is transmitted in a secure and unreadable format, even if intercepted by malicious actors.
Secure communication protocols, such as HTTPS, should be employed for all data transmissions within the production network. This extends to communication between machines, controllers, and any other components involved in the production process.
6. **Incident Response and Recovery Planning**
Despite robust preventive measures, the possibility of a cybersecurity incident cannot be entirely eliminated. Therefore, manufacturers must develop comprehensive incident response and recovery plans. These plans should outline the steps to be taken in the event of a security breach, including communication protocols, isolation procedures, and recovery strategies.
Regularly testing these incident response plans through simulated cyber attack scenarios ensures that personnel are well-prepared to handle real-world incidents effectively. Additionally, backups of critical data should be regularly performed and stored in a secure, isolated environment to facilitate rapid recovery in case of data loss or system compromise.
7. **Employee Training and Awareness Programs**
Human error remains a significant factor in cybersecurity incidents. Establishing a cybersecurity-aware culture among employees is crucial for minimizing the risk of social engineering attacks, such as phishing. Regular training programs should educate personnel about the latest cyber threats, best practices for secure behavior, and the importance of reporting any suspicious activities.
Employees should be vigilant about not only external threats but also potential insider threats. This dual focus ensures a holistic approach to cybersecurity within the organization.
Conclusion
As full-automatic block production systems become increasingly interconnected, the importance of robust cybersecurity measures cannot be overstated. Implementing a comprehensive cybersecurity strategy that encompasses network segmentation, access controls, continuous monitoring, software updates, encryption, incident response planning, and employee training is essential for safeguarding these critical manufacturing processes. By prioritizing cybersecurity, manufacturers can confidently embrace the benefits of automation and connectivity while fortifying their systems against evolving cyber threats.